24/7 Continuous Production Thermoforming Machines
24/7 Continuous Production Thermoforming Machines are pivotal in the manufacturing of plastic products, especially in the packaging industry. Designed for continuous operation, these machines can run 24/7, ensuring uninterrupted production and meeting high-demand requirements. Their robust construction and advanced engineering facilitate consistent performance, making 24/7 Continuous Production Thermoforming Machines indispensable for businesses aiming to maintain a steady supply of thermoformed products.
Table of Contents
The capability of 24/7 operation is particularly beneficial in industries where demand is constant, and downtime can lead to significant losses. By minimizing production interruptions, these machines enhance overall efficiency and productivity. This continuous operation is made possible through features such as automated controls, durable components, and efficient cooling systems, all of which contribute to the machine’s reliability and longevity.
Manufacturers like INPAK have recognized the importance of continuous production capabilities. Their Thermoforming machines are engineered to operate around the clock, providing businesses with the tools needed to meet the demands of modern production schedules. This commitment to continuous operation aligns with INPAK’s mission to deliver efficient and reliable thermoforming solutions to the plastic and packaging industries.
What Is Continuous Production?
Continuous production refers to a manufacturing process where production runs non-stop, 24 hours a day, seven days a week. This approach is typically employed for products with a consistent demand, allowing for uninterrupted production cycles. The primary goal is to maximize efficiency, reduce production costs, and ensure a steady supply of products to meet market needs.
In continuous production systems, the manufacturing process is streamlined to operate without significant pauses. This involves the use of automated machinery, continuous monitoring, and optimized workflows. The focus is on maintaining a consistent output, minimizing downtime, and ensuring that production aligns closely with demand forecasts.
Implementing continuous production requires substantial initial investments in machinery and infrastructure. However, the long-term benefits, such as reduced labor costs, increased production rates, and improved product consistency, often outweigh these initial expenditures. This production method is particularly suitable for industries dealing with high-demand, standardized products.
Features of Continuous Production System
Continuous production systems are characterized by several key features that contribute to their efficiency and effectiveness. One of the most prominent features is automation. Automated machinery and controls reduce the need for manual intervention, leading to consistent product quality and reduced labor costs. This automation ensures that production processes are carried out uniformly, minimizing human error and variability.
Another significant feature is the integration of real-time monitoring and control systems. These systems provide operators with immediate feedback on production performance, allowing for quick adjustments and maintenance. This proactive approach helps in identifying potential issues before they lead to significant downtime, thus maintaining the flow of production.
Flexibility is also a crucial aspect of continuous production systems. Modern systems are designed to accommodate changes in product specifications, allowing manufacturers to respond swiftly to market demands without extensive reconfiguration. This adaptability ensures that production can be adjusted as needed, maintaining efficiency while meeting varying customer requirements.
Continuous Production Plastic Food Container Machines
In the food packaging industry, continuous production thermoforming machines play a vital role in producing plastic food containers. These machines are designed to form plastic sheets into containers used for packaging food items, ensuring that the products are safe, durable, and meet regulatory standards. The continuous production capability ensures that these containers are produced in large quantities to meet the demands of the food industry.
The design of these machines allows for the use of various plastic materials, including PET, CPET, PP, PVC, PS, OPS, and PLA. This versatility enables manufacturers to choose materials based on the specific requirements of the food products being packaged, such as barrier properties, clarity, and sustainability considerations. For instance, INPAK’s thermoforming machines are compatible with these materials, providing flexibility in production.
Additionally, the precision of these machines ensures that the containers produced are consistent in size and shape, which is crucial for efficient packing, transportation, and storage of food items. Features like sensitive positioning and servo-driven transport chains contribute to this accuracy, enhancing the overall quality of the food packaging process.
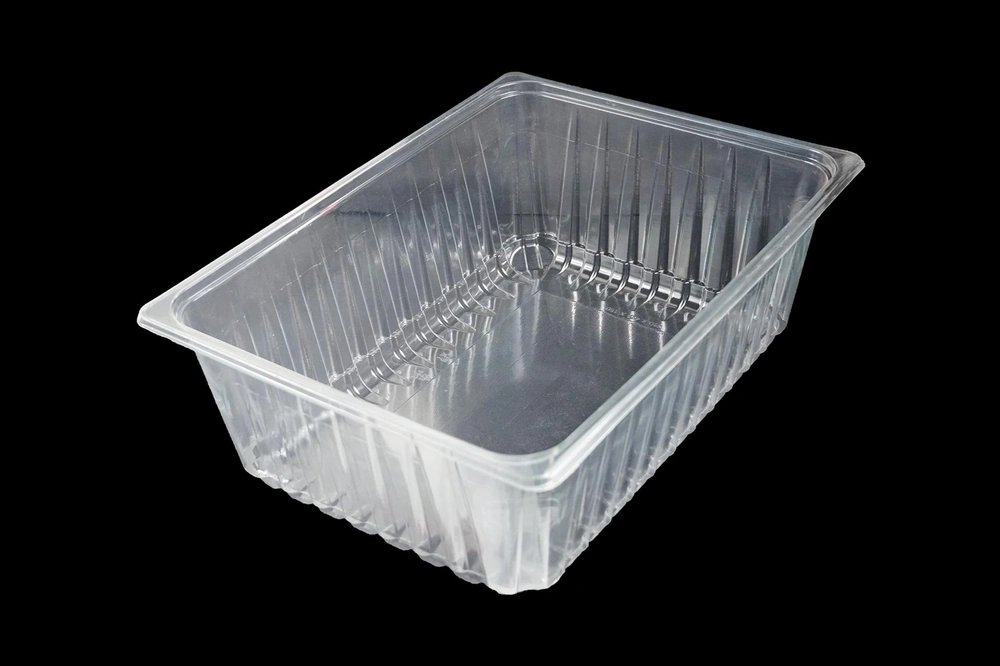
24/7 Continuous Production Thermoforming Machines
Advantages of Continuous Production with Thermoforming Machines
Utilizing continuous production with Thermoforming machines offers several advantages that enhance manufacturing efficiency and product quality. One of the primary benefits is increased production capacity. The ability to operate continuously allows manufacturers to produce large volumes of products, meeting high market demands without the need for additional shifts or overtime.
Another significant advantage is improved product consistency. Continuous production minimizes variations in product quality, ensuring that each item meets the desired specifications. This consistency is vital for maintaining brand reputation and customer satisfaction. Advanced features in thermoforming machines, such as automated lubrication systems and sensitive positioning, contribute to this uniformity.
Cost efficiency is also a notable benefit. By reducing labor costs through automation and minimizing material waste due to precise forming processes, manufacturers can achieve lower production costs. Additionally, the durability and reliability of modern thermoforming machines reduce maintenance expenses and downtime, further enhancing the cost-effectiveness of continuous production systems.
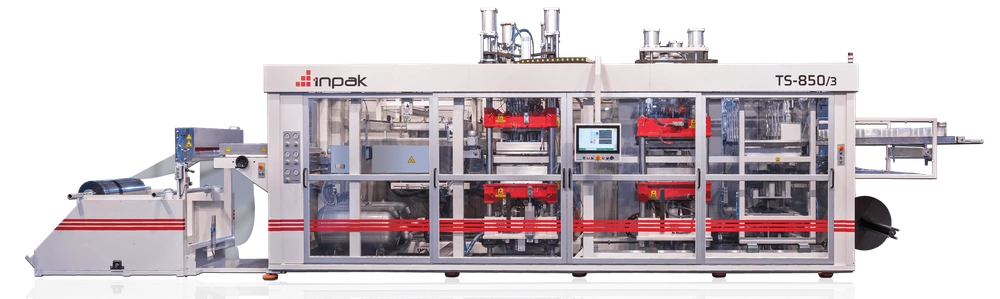
24/7 Continuous Production Thermoforming Machines
24/7 Operating Thermoforming Machines by INPAK
INPAK, a leading manufacturer of thermoforming machines, offers solutions designed for 24/7 operation, catering to the demands of continuous production environments. Their machines are built with high-performance components and advanced features to ensure reliable and efficient operation around the clock. For instance, the TSR-800 In-Mould Cutting Thermoforming Machine is designed for maximum mould dimensions of 800 mm x 580 mm and can achieve cycle speeds of up to 75 cycles per minute.