Differences Between Vacuum And Compressed Air Thermoforming Machines
What are the differences between vacuum and compressed air thermoforming machines? Thermoforming machines are essential in the production of plastic packaging, and they are commonly used across industries like food packaging and plastic products manufacturing. Two main types of thermoforming machines used for these processes are vacuum thermoforming machines and compressed air thermoforming machines. These machines serve the same purpose—forming plastic sheets into different shapes—but they use different mechanisms to achieve this.
Table of Contents
The key difference lies in the method of air pressure used in each type of machine. Vacuum thermoforming machines rely on creating a vacuum to draw the plastic sheet into the mold, while compressed air thermoforming machines use compressed air to push the material into the mold. Understanding the differences between these methods can help manufacturers choose the right machine for their production needs.
Both types of thermoforming machines have their advantages and disadvantages depending on the application. Vacuum thermoforming machines are often preferred for deep-draw molds, where the plastic needs to be pulled into intricate shapes. On the other hand, compressed air thermoforming machines are more suitable for applications requiring more even pressure distribution over the entire surface area of the material. What are the differences between vacuum and compressed air thermoforming machines?
What Are the Different Types of Thermoforming Machines?
Thermoforming machines come in various types, each tailored to specific manufacturing needs. The two primary categories are vacuum forming and compressed air forming, but there are also other types, such as pressure forming and multi-station thermoforming machines.
The choice of machine depends on the product being manufactured and the required quality of the final product. Vacuum forming machines are widely used for producing large, shallow items like trays and lids, while compressed air forming machines are more effective for creating deeper shapes where uniform air pressure is crucial.
There are also variations like cut-in-place thermoforming machines, which can trim the product in the same step as the forming process, making them ideal for high-speed, high-volume production.
What Are Vacuum Thermoforming Machines and What Are Their Applications?
Vacuum thermoforming machines operate by applying a vacuum that draws a heated plastic sheet into a mold. This process creates a tight fit of the plastic against the mold’s surface, making it ideal for shallow and intricate shapes. These machines are typically used in industries where precision and detailed shapes are important, such as in plastic packaging, particularly for products like food containers, blister packs, and cosmetic packaging.
The main advantage of vacuum forming is its ability to create highly detailed and accurate shapes. The process is also very efficient in terms of material use, as the vacuum creates a tight seal, minimizing excess material. However, it is less suited for very deep or thick-walled products, where a more even pressure distribution is required.
What Are Compressed Air Thermoforming Machines and What Are Their Applications?
In contrast, compressed air thermoforming machines use compressed air to push a heated plastic sheet into a mold. This method is more suitable for producing thicker and deeper parts. Compressed air forming works by inflating the sheet, allowing the air to push the material into the mold more uniformly than the vacuum process.
These machines are often used in applications that require deeper draw depths, such as in the production of large containers, automotive parts, or other complex shapes that need uniform pressure distribution across the entire surface. The compressed air process can handle thicker materials, making it ideal for creating products that need more structural integrity.
How Do Vacuum Thermoforming Machines Work?
The process of vacuum forming starts with heating a plastic sheet until it becomes pliable. Once the plastic is heated to the optimal temperature, it is stretched over a mold. A vacuum is then applied to remove the air between the sheet and the mold, drawing the material tightly into the mold’s shape. This process is ideal for creating items that require detailed molding with smooth surfaces.
The main steps in vacuum thermoforming include heating the plastic, forming the plastic sheet over the mold, and then trimming the excess material from the formed part. The vacuum creates a stronger bond between the plastic and the mold, ensuring high precision. The method is efficient and cost-effective for producing shallow parts.
How Do Compressed Air Thermoforming Machines Work?
Compressed air thermoforming machines differ by using compressed air to press the heated plastic sheet into the mold. After heating the plastic, the air is pumped into a cavity beneath the sheet, forcing the plastic into the mold’s shape. The compressed air method distributes pressure more evenly across the plastic, making it ideal for deeper forms and thicker materials.
This process allows for more flexibility when forming larger parts and provides better uniformity in material distribution. The compressed air also helps minimize the risk of wrinkles or stretching, which can sometimes occur in vacuum forming when deeper draws are needed. The result is a more reliable and consistent product, particularly in industries like automotive or packaging.
What Are the Key Differences Between Vacuum and Compressed Air Thermoforming Machines?
The primary difference between vacuum thermoforming and compressed air thermoforming lies in the method of air pressure used to form the plastic. Vacuum thermoforming is most effective for shallow molds and applications where precision in surface details is essential. The vacuum pulls the plastic tightly into the mold, making it perfect for packaging solutions, such as plastic packaging machines for food or consumer products.
In contrast, compressed air forming excels in producing deeper, more complex shapes. The use of compressed air allows for more even pressure distribution, making it ideal for creating thicker-walled or deeper products, such as automotive parts or larger containers. The process also works better with a wider range of material thicknesses.
What Should You Consider When Choosing a Thermoforming Machine?
When choosing between vacuum forming and compressed air forming, it is essential to consider the depth of the mold, the material being used, and the required precision of the finished product. If your application requires detailed, shallow molds, a vacuum thermoforming machine is likely the best choice. For deeper parts with thicker materials, compressed air forming machines would be more suitable.
Other factors include the production volume, the cost-effectiveness of each method, and the specific requirements of the product. Thermoforming machine production should be aligned with the manufacturing goals, whether it’s for plastic packaging machines, food packaging, or other applications requiring custom molded plastic products.
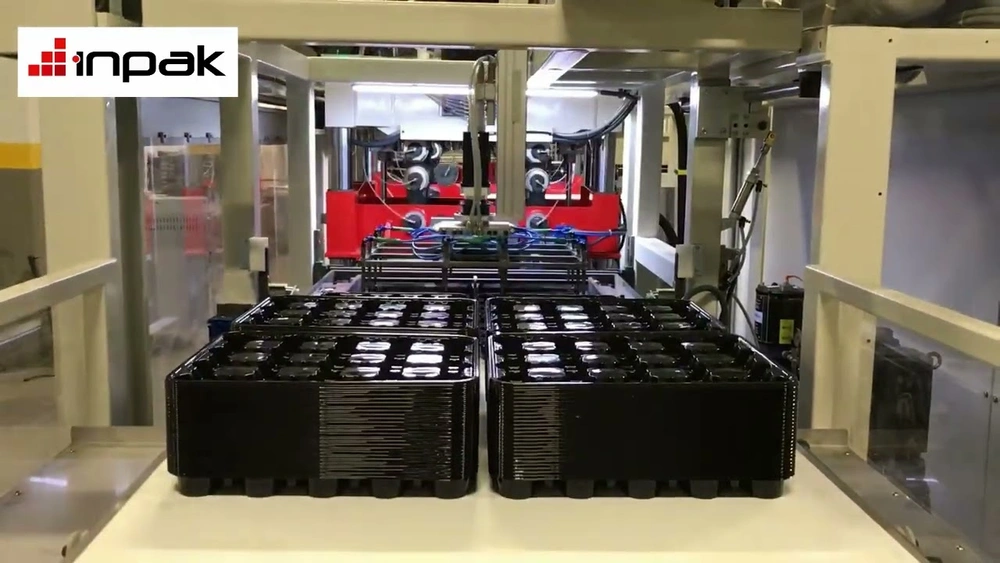
Differences Between Vacuum And Compressed Air Thermoforming Machines
Inpak Machines: High-Efficiency Thermoforming Machine Solutions
INPAK, as a leading thermoforming machine manufacturer, offers high-efficiency machines that cater to various industrial needs. Whether you require vacuum forming or compressed air forming, INPAK machines are designed to optimize production processes and deliver consistent, high-quality results. INPAK’s commitment to sustainability and efficient manufacturing makes it an ideal choice for businesses in the plastic packaging and food packaging sectors. INPAK enhances production processes with high-tech thermoforming machines by automating operations, providing businesses with low labor costs and high return on investment (ROI). Thanks to fully automated systems, the need for manual labor is minimized while production capacity and efficiency reach maximum levels. This enables businesses to gain significant advantages in terms of both time and cost.
Thermoforming machines capable of operating 24/7 allow for the continuous, fast, and high-quality production of plastic products. With low energy consumption and high production speed, they offer an eco-friendly and sustainable manufacturing process. INPAK develops effective solutions for various production demands by manufacturing machines that can be customized according to each customer’s specific needs.
Featuring a durable design with a low risk of malfunction, the machines ensure long-term use and reduce maintenance and repair costs. This decreases operational expenses and increases profitability. Committed to continuous improvement, INPAK maintains its leadership in the industry by offering the best thermoforming machine solutions in terms of speed, quality, and efficiency.