
By the end of 2023, Inpak has expanded its global presence to 50+ countries, where our machines are in operation. We’ve achieved solid milestones, including reducing aftersales income from %1.3 to %1.2 of total revenue, with ongoing efforts to decrease it further! The repeat order ratio for delivered machines reached an impressive %80 this year, and we successfully increased the total number of clients by %8. Inpak’s contribution to Turkey’s export in the field remains strong at %65.
The recent acquisition of Euromak, known for delivering high-quality performance moulds, empowers clients to receive complete projects while maximizing the sustainable use of Inpak machine features.
The second year of managerial team workshops, guided by our executive coach, has been completed, promising long-term contributions to the company. Inpak is strategically developing an organic structure by minimizing 3rd party solution agreements, ensuring better customer satisfaction through direct monitoring of all sales and after-sales cases.
Post-pandemic, we are transitioning back to just-in-time storage management, minimizing operational costs, thereby allocating an increased budget to continuous Research and Development. This approach helps in reducing Euro-based inflation effects in our sales agreements while maintaining industry expectations.
Despite industry challenges, Inpak is a growing force in thermoforming, dedicated to ensuring client success through reliable, optimal engineering for the highest return on investment and continuous high efficiency over longer lifetimes. Our commitment extends to delivering operational satisfaction to our clients. We advocate for sustainable plastics packaging production, validated by solid life cycle assessments that confirm its environmental friendliness, emphasizing the importance of well-implied recycle, reuse, and renew processes.
Having reached full production capacity, we eagerly anticipate moving into our new factory in 2025. Our proactive measures to functionally support Inpak’s potential growth encompass all operational aspects to ensure long-term alignment with KPIs. We express gratitude to our valued employees and clients worldwide for their continued support.
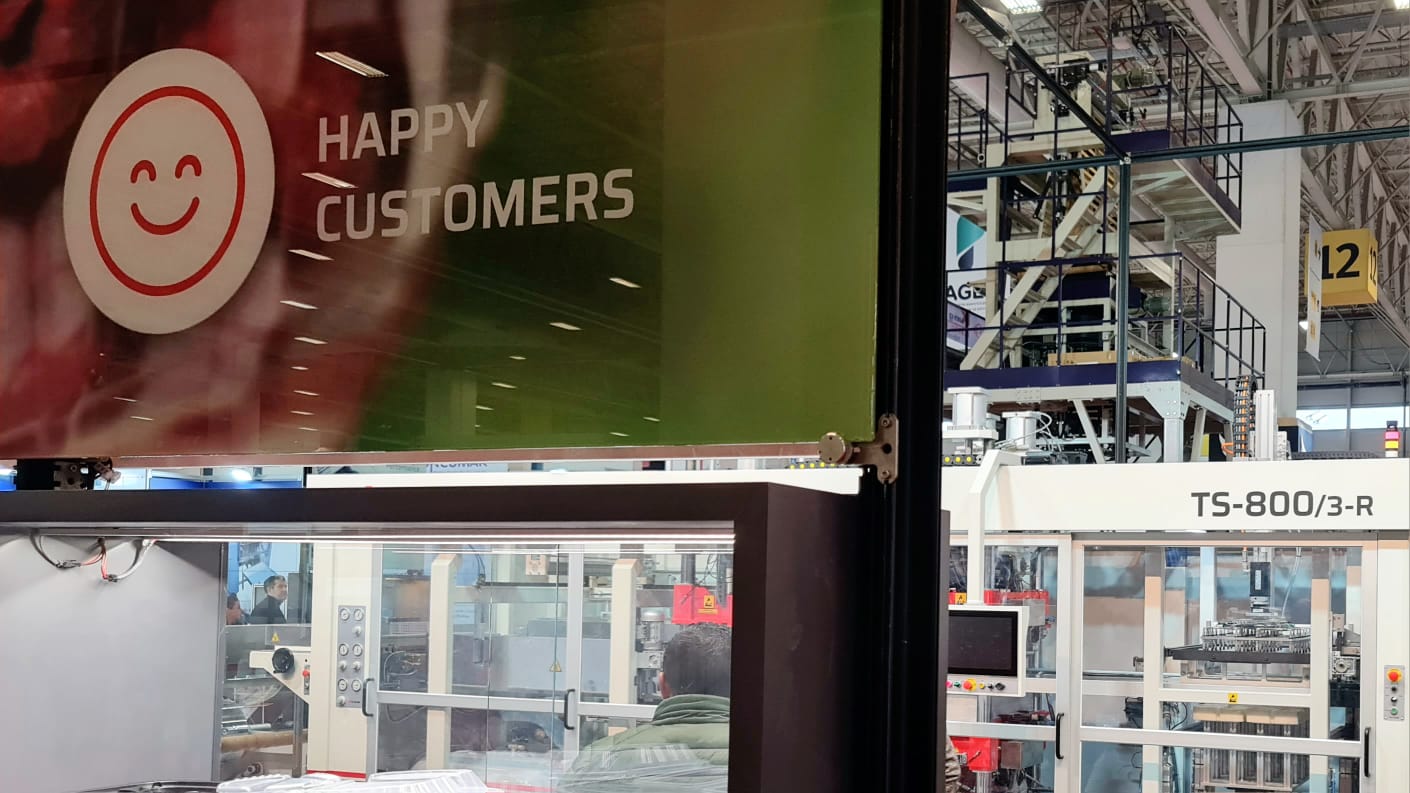
Inpak had contributed its insights to an article discussing the dynamic trends within the plastic packaging and thermoforming industry. We covered important topics such as risk management in the organisation, providing inreased efficiency, being environmentally conscious about materials, the growing demand for automation, and our plans for planned growth.
Thanks to Steven Pacitti the editor of Eco-Plastics in Packaging, for having our perspective featured in this insightful article.
Efficiency and Resilience in Thermoforming Business
The journey hasn’t been without its challenges. We’ve encountered difficulties such as doubling lead times due to heightened demand and supply chain complexities. Yet, our team’s risk management has put us forward, addressing issues such as component availability and optimizing stock management.
Efficiency Incresement in Inpak machines
Energy efficiency is not just a trend for us—it’s a part of continuous developemt that provides competitor advantege tou our packaging producer partners. Through redesigns on the existing systems, we’ve achieved an impressive 5% increase in efficiency.
Sustainability Matters
Inpak heating and forming cacpabilites are ok to run fossilbased or biobased thermoformable, recyclebale and compostable materials. Since the critical path is related with collecting, separating and recycling of the materials, we’re actively engaged in materials that are like PET, rPET, and PP for a greener future for the packaging industry.
Increasing need for Automation
As the demand for automation grows, particularly in regions with high labor costs, Inpak has been following the industrial developments offered by speciliesed 3rd part companies, hoping that a pioneer in embracing this change. We’re working towards smarter solutions that elevate efficiency across our operations.
Expansion and Growth
The horizon is expansive for Inpak Thermoforming. Plans are underway for a new manufacturing facility, a testament to our unwavering dedication to meeting growing demands while fostering innovation and excellence.
Read the full article: https://www.linkedin.com/embed/feed/update/urn:li:ugcPost:7102961801226563584
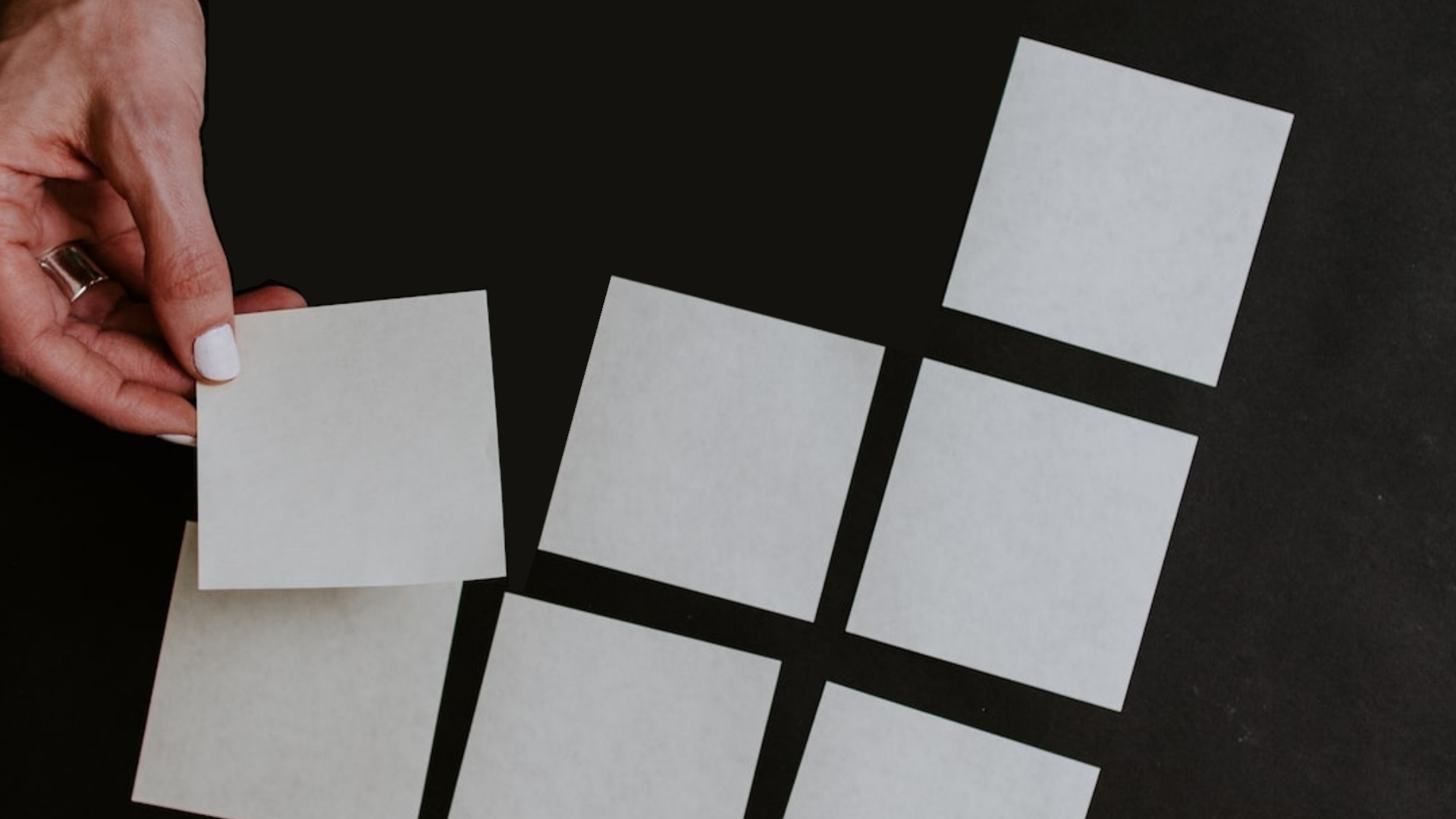
At Inpak, we value open communication and believe in providing our customers with all the necessary information available at their fingertips.
We are glad to announce the publication of our Frequently Asked Questions (FAQs) section, dedicated to providing you with more detailed knowledge about Inpak’s globally recognised thermoforming machines. These FAQs have been curated to address common queries and offer insights into the features, capabilities, and benefits of our thermoforming machines.
Whether you’re new to thermoforming or a professional seeking advanced solutions for your packaging requirements, our FAQ guide serves as an informative resource to help you understand the fundamental approaches of Inpak prior to your detailed assessments with our business development team.
Discover the answers to a wide range of questions, including offered thermoforming machine types, forming capabilities and tooling dimension limits, brief info about Inpak and servicing. And many more!
We look forward to assisting you in making the optimal choice for your business.
Visit our FAQs now: https://www.inpakmakina.com/frequently-asked-questions/
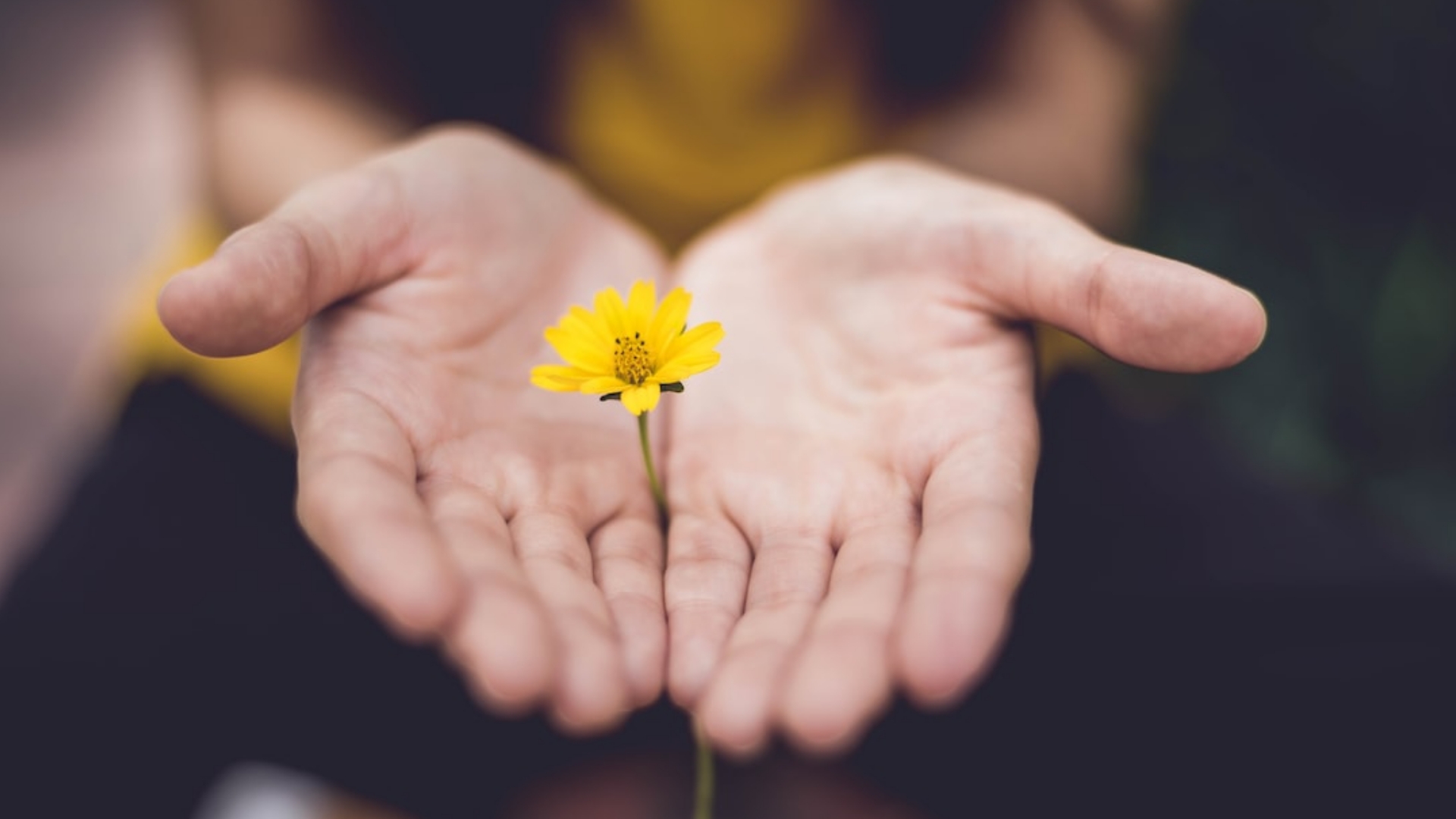
Inpak marketing and business development team conducted a customer survey to understand deeper why repeat customers choose our brand and solutions with a loyalty rate of 94%. The results of the survey revealed key factors for the customer loyalty of its repeat orders.
Long machine lifetime
The survey found that a remarkable percentage of repeat customers continue to choose Inpak’s thermoforming machines because of its reliability and long machine lifetime. In fact, Inpak’s very first machine, with serial number 001, is still in active use today, which is a testament to the longevity of the machines. Inpak machines are designed and built to withstand 24/7 usage, engineering to ensure reliable performance for many years.
Service speed and its effectiveness
Customers find reliable service, support and consultancy in after sales period. Inpak’s technical team is dedicated to providing quick and efficient support to customers, ensuring increased availability in production. This customer centric approach has helped to earn the loyalty of repeat customers.
Net running time of the machine
Inpak thermoforming machines also stood out for its high net running time for extended periods. Inpak’s machines are built to perform at optimal levels, providing customers with maximum efficiency and productivity. This reliability with high OEE enables competitive advantage in the market.
Mould providing support
Inpak offers experienced mold solutions and support for packaging production, catering to the needs of the food, agriculture, and cosmetics industries. Inpak’s experienced team works like in-house department of customers to meet specific production requirements, ensuring that customers can achieve their production goals with a long-lasting mould lifetime.
Configuration variety
Inpak’s ability to provide a wide range of machine configurations also has been attractive to customers. Inpak’s engineering team works closely with customers to design and build machines that meet their unique needs, which has helped to earn their loyalty as well.
Brand image
Finally, our globally recgonised, positive brand image which is gained power by high satisfying customer experience has helped to build customer trust and continuous partnerships.
In general, the survey revealed that repeat customers are highly satisfied with Inpak’s thermoforming machines and solutions. Key factors such as Inpak’s commitment to providing value for money, reliability, and exceptional customer experience have earned the trust and loyalty in repeat customer orders, cementing our position in the global thermoforming machinery industry. We thank our customers for being our partners.
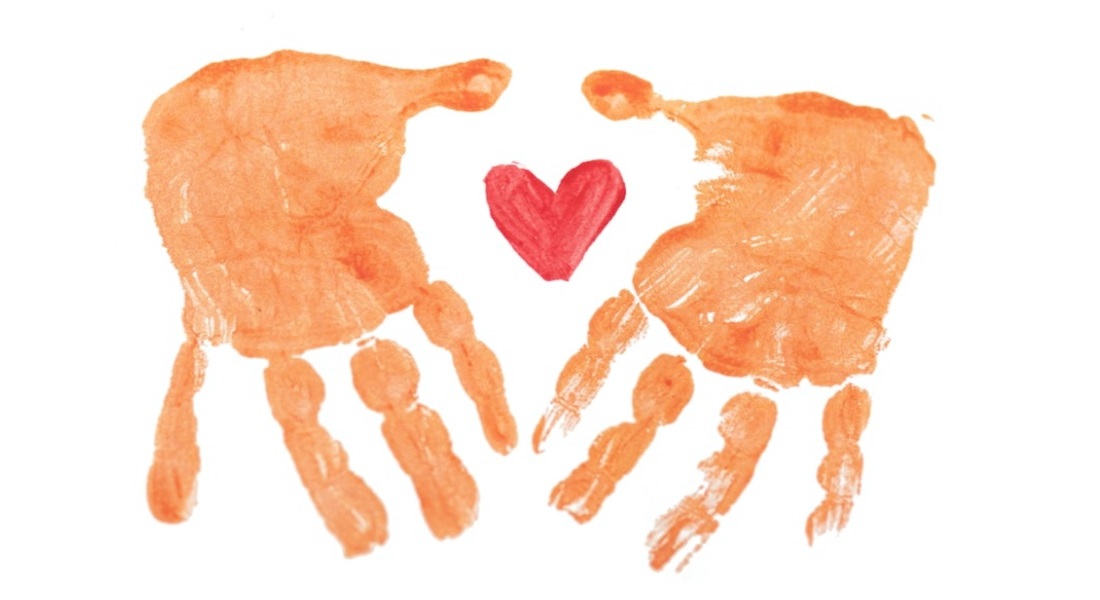
Open call to packaging producers: We all see and understand the significance of helping our communities in times of need.
The earthquake based in Kahramanmaras and affected 10 cities was a major natural disaster. Thankfully, as Inpak family we are fine. However, it is devastating for the affected regions and our hearts. It left people without basic necessities such as food, water, and shelter. Providing aid became a major challenge, and it is essential that we come together as a community to support those in need.
We encourage our customers to consider donating recyclable plastic packaging to aid organizations and charities for the people in the affected regions by the earthquake. We believe that our customers can play a critical role in helping to address the needs of those affected by the disaster. As Inpak, we aim to provide our support in the procurement of the necessary thermoforming machines and resources in the goal oriented projects for the food packaging production.
Recyclable plastic packaging can provide a level of protection and convenience for the needs, while also ensuring that waste is minimized and resources are used as efficiently as possible. We believe that by working together, we can help make a positive impact on the lives of those affected by the earthquake.
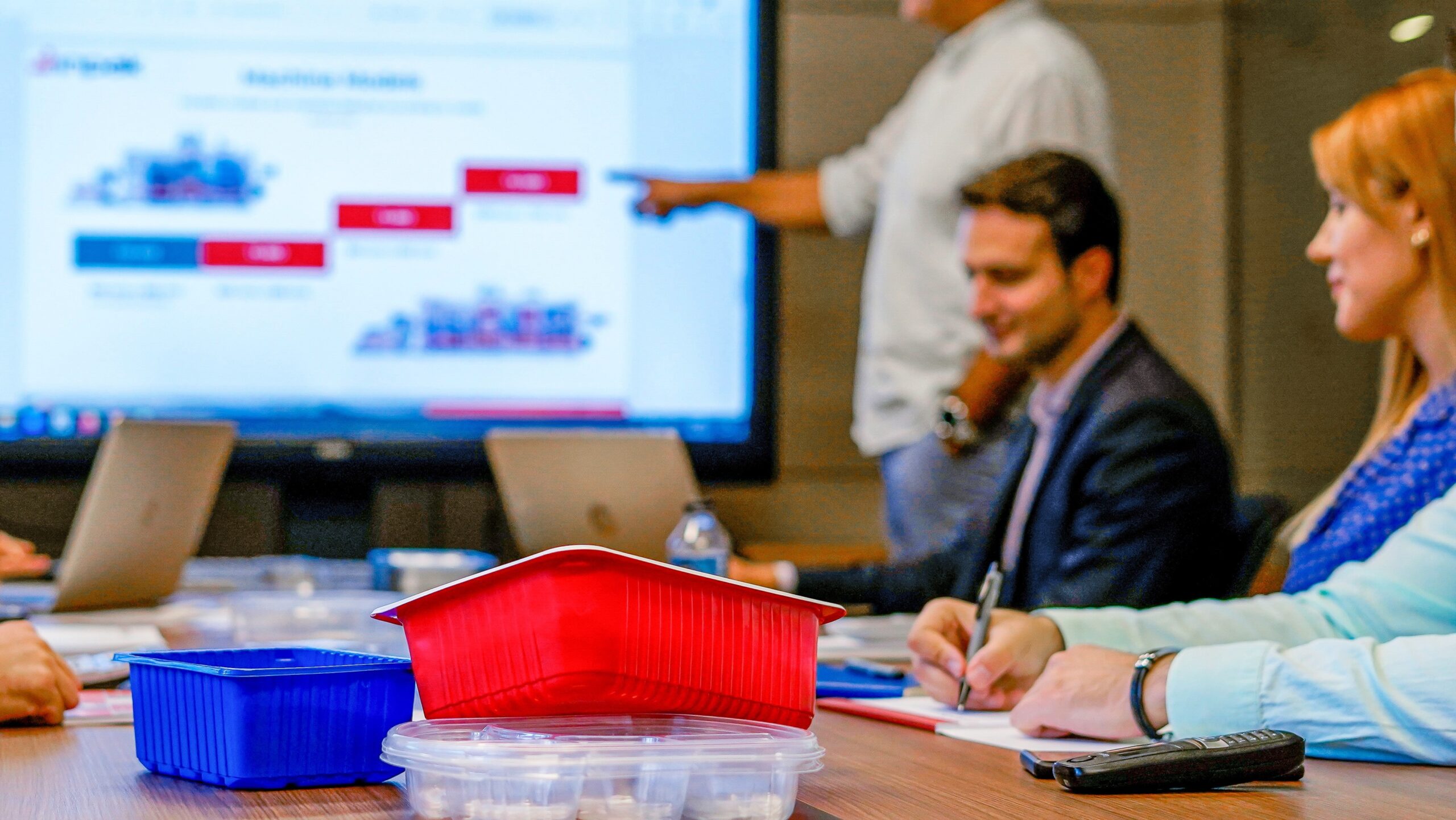
For our visitor’s easy and fast access to information related to Inpak and our machines, we renew our website. Hope you liked it.